在無錫液壓機進行深拉伸工藝時,防止工(gōng)件出現起皺、拉裂等缺陷需從多方(fāng)麵著手。
模具設計是關鍵因素。對(duì)於(yú)深拉伸模具,合理設計凸模和凹模的圓角(jiǎo)半徑非常重要。凸模圓角(jiǎo)半徑過小,會使材料在拉伸過(guò)程中受到的局部應(yīng)力過大,容易導(dǎo)致拉裂;凹模圓角半徑過小,則會增加材料流動的阻力,引發起皺。一般來說,凸模圓角半徑可取值為工件厚度的 3 - 6 倍,凹模圓角半徑為(wéi)凸模(mó)圓(yuán)角半徑的 1.5 - 2 倍。同時,要保證模具表麵的光潔度,降(jiàng)低表(biǎo)麵粗糙度,減少(shǎo)材料與模(mó)具之間的摩擦力,有利於材料均勻流動,防止起皺和拉裂。
壓邊力的控製對拉伸質(zhì)量影響顯著。壓邊力過小,無法有效抑製材料的起皺;壓邊力過大,則會使材料流(liú)動困難,增(zēng)加(jiā)拉裂的風險。在實際生產中,可(kě)根據材料的厚度、材質以及拉伸工(gōng)藝要求,通過調試(shì)確定合適的壓邊力。例如,對於較薄的金屬板材,壓邊力可適當減小;對於高強度材料,壓邊力需(xū)相應增大。采用可調節的(de)壓邊裝置,如液壓式壓邊圈,能夠在拉伸過(guò)程(chéng)中根(gēn)據材料的變形情況實時調整壓邊力(lì),更好地保證拉伸質量。
拉伸速度的選擇也不容忽視。拉伸速度過快,材料來不及均勻變(biàn)形,容易在局部產(chǎn)生應力集中,導致拉裂;拉(lā)伸速度過慢,則會影響(xiǎng)生產效率。一般情(qíng)況下,對於深拉伸工藝,拉伸速度可控製在每分鍾 5 - 15 次左右。同時,要保持拉伸過程的平穩性(xìng),避免速度突變,可通過優化液壓係統的控製,實現滑塊(kuài)速度的穩定調節。
潤滑條件對防止缺陷也(yě)起著重要作用。在拉伸過(guò)程中,在模具與工件之間塗(tú)抹合適的潤滑劑,能夠有效降(jiàng)低摩擦(cā)力,減少材料(liào)的磨損,同時有助於材料均勻流動。常用(yòng)的潤滑(huá)劑有拉伸油、乳(rǔ)化液等,應(yīng)根據材料的材質和(hé)拉伸工藝要求選擇合適的潤滑劑。例如,對於不鏽鋼材料的(de)深拉伸,可選用含有特殊添加劑的拉伸油,以提高潤滑效(xiào)果和防腐蝕性能。在塗抹潤滑(huá)劑時,要確保(bǎo)均(jun1)勻覆蓋模具和工件表麵,尤其是容(róng)易出現起皺和拉裂的部位。
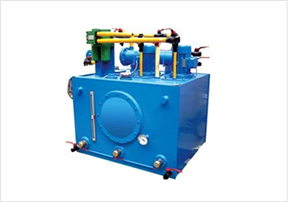