模具在無錫(xī)液壓機使用過程中出現磨損,原因較為複雜。
從模具材料角度看,若模具材料本身硬度不足或耐磨性差,在頻繁承受高(gāo)壓和摩擦的情況下,極易出現磨損。例(lì)如,對於一些需要(yào)衝壓高(gāo)強度金(jīn)屬材料的模具,如果(guǒ)選用了硬度較低的模具鋼,可能在短時間內(nèi)就會出現明顯磨損。解決辦(bàn)法(fǎ)是根據所加工材料的特(tè)性(xìng),合理選擇模具材料,對於加工高(gāo)強度材料,應選(xuǎn)用高硬度、高耐磨性的(de)模具鋼(gāng),如 Cr12MoV 等(děng)。
模具的設計(jì)結構也會影響磨損情況。如果模具的脫模斜度不合理,工件在脫模過程(chéng)中與模具表麵的摩擦力增大,會(huì)加速(sù)模具磨損。比如脫模斜度過小,工件緊緊貼合在模(mó)具(jù)表麵,脫模時需(xū)要(yào)較大的外力,這會對模具表麵造成嚴重刮擦。此時需要對模具結構進行優(yōu)化(huà)設(shè)計,根據工件形狀和尺寸,合理確定脫模斜度,一般來說,脫模斜度在 1° - 3° 較為合適,以減少脫(tuō)模阻力(lì),降低模具磨損。
在加工過程中,工藝參數選擇不當也是導致模具磨損的重要原因。壓力過大,會使模具承受(shòu)過高的載荷,加速模具表麵的疲勞磨損;速度過快,會使模具與工件之間的(de)摩擦加劇,產生(shēng)大量熱量,導致模具局部溫度(dù)過高(gāo),硬度下降,從而加速磨損。應根據工件材料和厚度,調整液壓機的壓力(lì)和速度。例如,對於較薄的金屬板材衝壓,適當降低壓力和速度,既(jì)能(néng)保證加工質量,又能減少模(mó)具磨損。
當模具出現磨損後,可采取不(bú)同修複措施。對於輕微(wēi)磨損,如表麵劃痕、擦傷等,可采用打磨(mó)拋光的(de)方法,使用砂紙(zhǐ)、砂輪等工具對磨損部位進行精細打磨,去除表麵的損傷層,恢複模具表麵的光潔度。若磨損較為嚴(yán)重,導致模具尺寸精度下降,可采用補焊的方法進行修複。選用與模具材(cái)料相匹配的焊條,對磨損部位進行補焊,然後再(zài)進行機械加(jiā)工,如車削、磨削等,使(shǐ)模具恢複到(dào)原來的尺寸精度。對(duì)於一些關鍵部位的嚴重磨損,若修複成本過高或無法修複(fù),應及時更換新的模具,以保證(zhèng)生產的正常進行和產品質量。
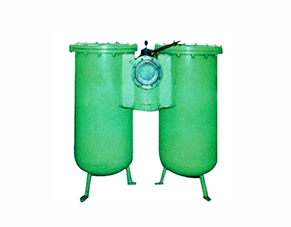